Produced by 3 fully-computerized batching plants, CSI assures clients of better quality concrete. CSI Ready Mixed Concrete Division is an ISO 9001 certified plant. It has over 60 transit mixers and fleet of concrete pumps for efficient and continuous delivery. It is also equipped with a chiller for a cooler and better concrete.
3 Fully Computerized Batching Plant
That raises the level of excellence in product quality and performance. CSi-North Plant has a total capacity of 160 cu.m. per hour while South Plant has a capacity of 100 cu.m. per hour.
State-of-the-Art Laboratory
That is composed of experienced professionals who provide quality products and services.
That ensures dependable and prompt deliveries.
That is composed of experienced professionals who provide quality products and services.
That is used for easy pumping of concrete mix in high-rise pouring structures.
Capable to produce 4◦C chilled water. That reduces the problem on high concrete temperature, which affects fresh and hardened concrete.
At the forefront of CSI’s commanding lead are ONEDAY MD3000/2000-60 MC and GENESIS 80 WETBETON, the plants are designed and produced by companies known in the world as prominent manufacturers of concrete batching plants.
GENESIS 80 WETBETON’s salient features include the BETONSYSTEM, a control system that applies electronic and data processing technology to control the concrete mixing plant and MIXER MIND, helps monitor the quality of concrete and its slump level while ONEDAY MD3000/2000-60 MC has a feature of FAST WEIGHING SYSTEM.
Anticipating the future demand of high-performance concrete in Cebu, CSI engineers work to improve its design mixes and challenge current designs. CSI can deliver 15,000-psi concrete. CSI’s research and development group are working on 20,000-psi design to satisfy future demand. CSI is recognized in the market to provide high-early strength concrete for the purposes of reducing construction time or permit rapid opening of roads to traffic. High-early strength concrete designs that were produced and delivered to various clients were 3,500-psi at 18 hours, 6,000-psi at 3 days, and 3,000-psi at 24 hours and 3,500-psi at 39 hours. CSI management constantly works to develop and realize what they believe is the most comprehensive and visionary approach in the ready-mixed concrete industry.
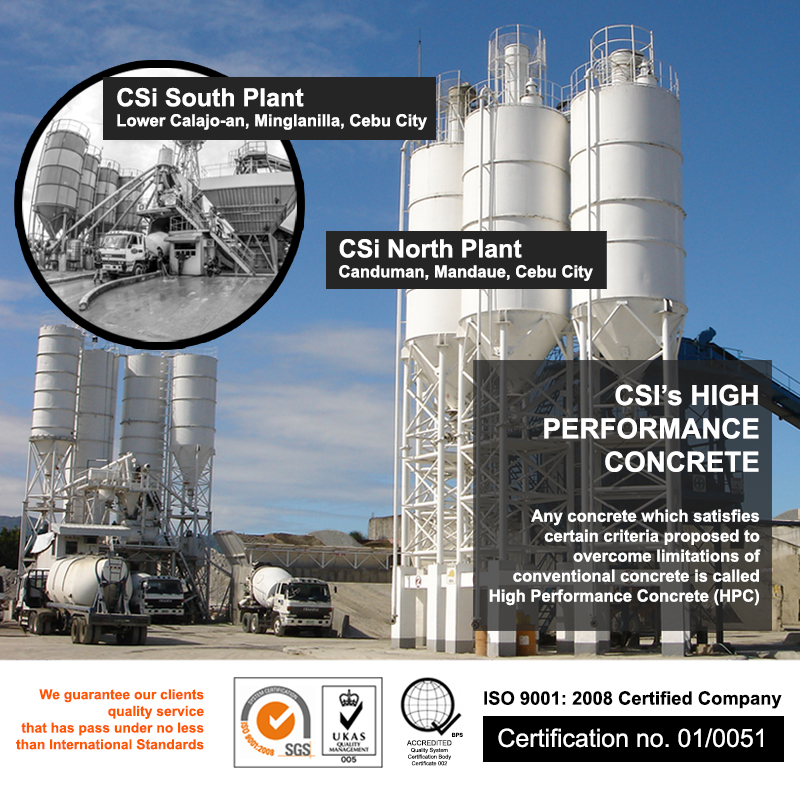